PRODUCTION TECHNOLOGY
The manufacturing of technical ceramics requires highly developed processing machinery in order to ensure rational production and a constant high quality.
Bettini produces all its materials by itself to keep the product quality under control and supply its customers with the best service (e.g.: to enable use of the same equipment, moulds etc. with different material types).
The following flow chart shows the production process for ceramic materials.
It is divided into 5 main moulding lines:
Cold isostatic pressing
Extrusion
Dry pressing
Injection moulding
Hot pressing
|
 |
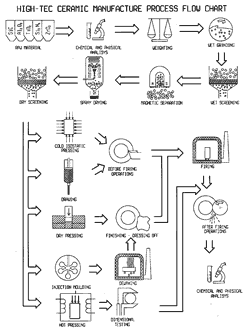 |
The main steps of the ceramic production are:
1) Production of ceramic granulate of required dimensions. - The raw material is first wet-ground in a ceramic ball mill to produce a slurry, then dried and granulated in spry drying equipment through fountaine spray drying and centrifugal spray drying.
Different binder are added to the granulate for injection moulding and extrusion.
2) Moulding - Ceramic granulate is loaded into a mould or cavity and a pressure is applied.
This operation gives the piece enough strength to be handled. In this step the pieces are called green, meaning non-sintered.
3) Sintering. Green parts are heated just under the melting temperature (1350°C 2100°C) in kilns in natural atmosphere for oxides, and in controlled atmosphere for non-oxides. During this process the grains weld together, giving the piece its final resistance.
For hot pressing, steps 2 and 3 are simultaneous.
4) In many cases further finishing operations are carried. The fired parts are machined to obtain narrow and/or extra-fine finishings. Grinding, lapping and polishing are performed with diamond tools.
|